O primeiro carro elétrico português faz-se em Mangualde, na fábrica com 63 anos, a mais eficiente entre dezenas da Stellantis por todo o mundo. Fomos lá procurar o segredo do sucesso.
Que a Autoeuropa vai ter um automóvel ligeiro de passageiros 100% elétrico já é sabido, mas o que poderá surpreender alguns é que não é necessário esperar por 2027 (data prevista para o citadino da VW) para ter um carro elétrico made in Portugal. Ele já está a ser produzido, e o ECO/Local Online acompanhou o fabrico de um deles.
Com logótipos de marcas alemãs, francesas e italianas, o modelo produzido na fábrica da Stellantis de Mangualde é o primeiro 10% elétrico feito em Portugal com cinco lugares, inserindo-se numa produção anual que este ano deverá atingir 92 mil unidades, num volume de negócios anual de praticamente mil milhões de euros.
Esta fábrica, fundada no início dos anos 60 do século passado, e a última onde se produziu o Citroën 2 CV a nível mundial, há 35 anos, é a segunda maior da indústria automóvel portuguesa, só superada, precisamente, pela Autoeuropa. E é aqui, em Mangualde, que vamos conhecer o primeiro automóvel ligeiros elétrico de produção em massa em Portugal.
O desenho da autoestrada A25 deixou a fábrica da Stellantis a menos de dois quilómetros de distância, e para que não restem dúvidas de que estamos no caminho certo quando saímos desta autoestrada, somos recebidos pela rotunda onde está esculpido, em alto-relevo, o inevitável Citroën 2 CV.
Quando perguntamos aos responsáveis da unidade fabril do grupo industrial franco-italiano-americano qual a última unidade do 2 CV produzida em Mangualde, ninguém nos sabe dizer ao certo. Em julho de 1990, alguém decidiu colocar uma matrícula com inscrição “Último 2 CV” numa unidade e outra com “Dernière 2 CV” noutra unidade, gerando um enigma sem solução. Arriscamos uma forma de resolver a contenda: o “dernière” 2 CV é aquele de granito na rotunda, inaugurado no final de julho em 2010.
Nesse mesmo dia, além do anúncio de reabertura do terceiro turno de produção e criação de 300 postos de trabalho — após o despedimento de cerca de 500 pessoas no ano anterior e passagem a dois turnos, momentos de receio pela sobrevivência desta unidade satélite da que existe em Vigo, na Corunha, Espanha —, a fábrica ganhou de presente do Estado um troço da Estrada Nacional 16, numa reta que separa o polo inicial da fábrica do terreno onde se ergueu um segundo bloco fabril em 2006.
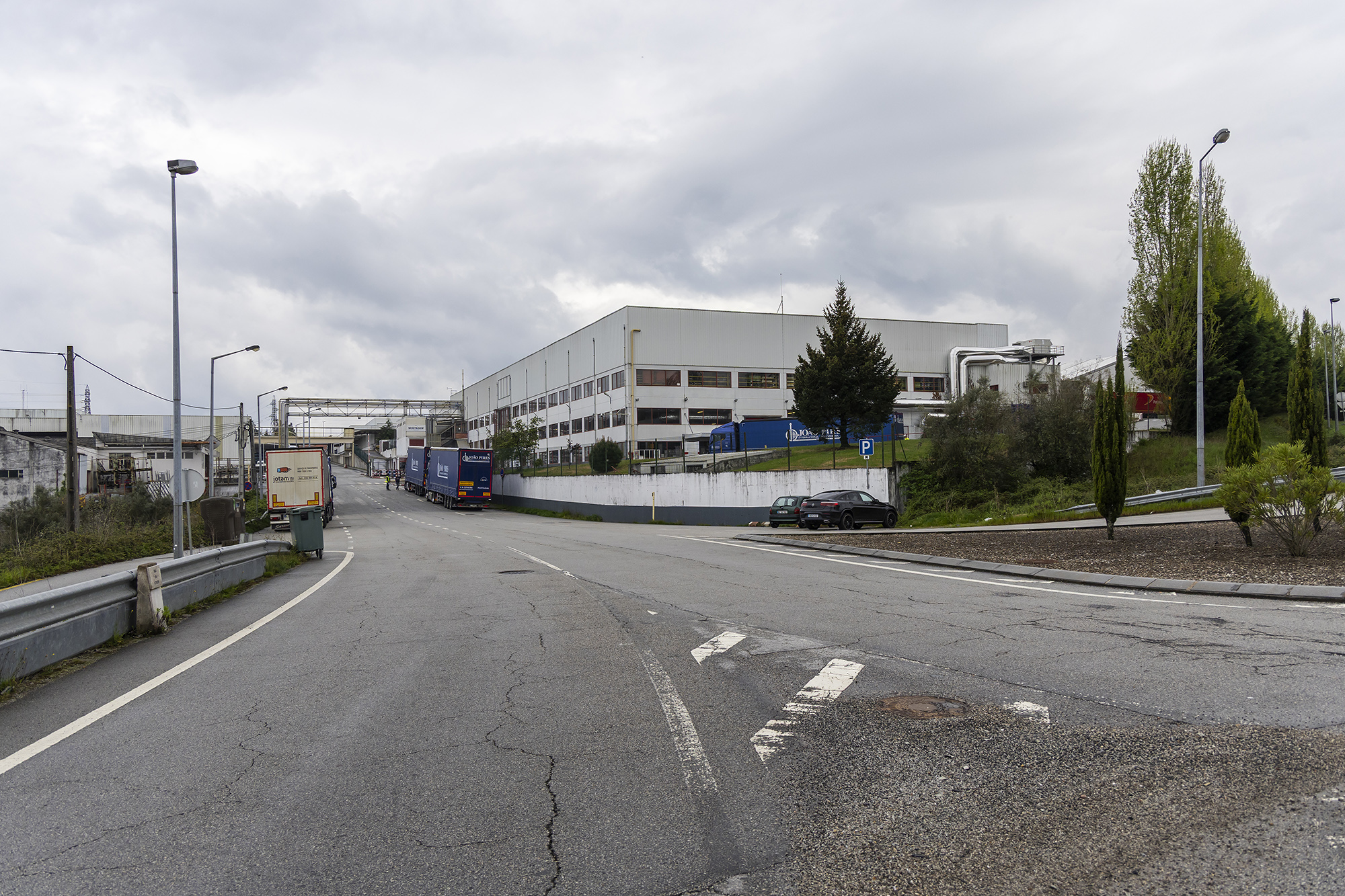
É precisamente por esse troço retirado à rede nacional de estradas que acedemos ao recinto do centro de produção Stellantis Mangualde. A fábrica que hoje vemos teve no ano passado a sua mais recente renovação, uma área de 800 metros quadrados para acomodar a produção das versões 100% elétricas dos modelos das quatro marcas aqui produzidas.
Além dos pavilhões principais, haverá, em breve, um novo edifício para preparação das viaturas, um investimento que evitará a atual deslocação para instalações fora da fábrica. Outra estrutura a desenvolver será um parque para viaturas junto à estação de caminhos de ferro, onde a Câmara de Mangualde tem um terreno à disposição da Stellantis, conta-nos o diretor da unidade, Múcio Brasileiro, que guia o ECO/Local Online pela fábrica que lidera há dois meses.
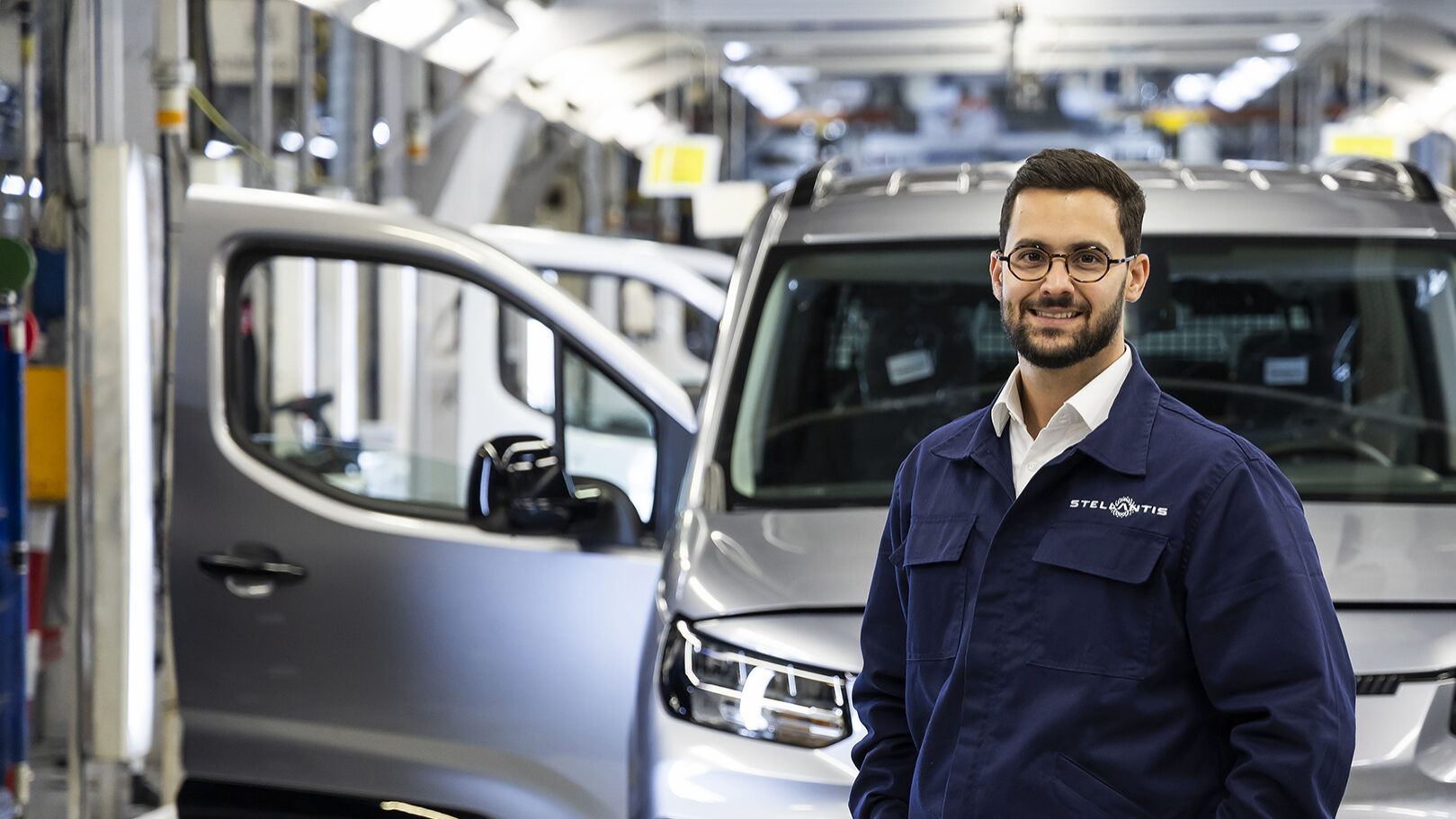
Essa mesma linha férrea servirá, logo que seja reaberta após anos de obras, para um teste de expedição dos automóveis de exportação por comboio, em direção a um porto do Norte de Portugal.
Considerando a “privatização” do troço da EN 16, os automobilistas passaram a usar uma estrada alternativa, mas não há relato de contestação entre a população de Mangualde. A fábrica, explica ao ECO/Local Online o trabalhador com mais anos de laboração, tem um papel agregador na comunidade, num espírito de família. “É muito importante para a nossa pequena cidade. Se não fosse a fábrica, provavelmente teria emigrado, ou ido para uma cidade maior”, diz José Ferreira, que este ano completará três décadas na divisão de pintura.
“Quando entrei na empresa, em [19]95, era da Citroën. Havia só um turno [de produção]. Comecei a pintar o AX, era tudo manual, não havia cá robôs. Depois, o Saxo e a seguir veio a nossa joia, a nossa Berlingo”, recapitula.
Hoje, José é um dos cerca de 900 trabalhadores que formam os três turnos necessários para assegurar mais de 90 mil veículos por ano. Já o Berlingo é um dos quatro modelos que daqui saem, e leva no curriculum o segundo lugar nas vendas mundiais da Citroën durante vários anos. Além de Mangualde, também Vigo o produz, tal como aos restantes modelos daqui saídos.
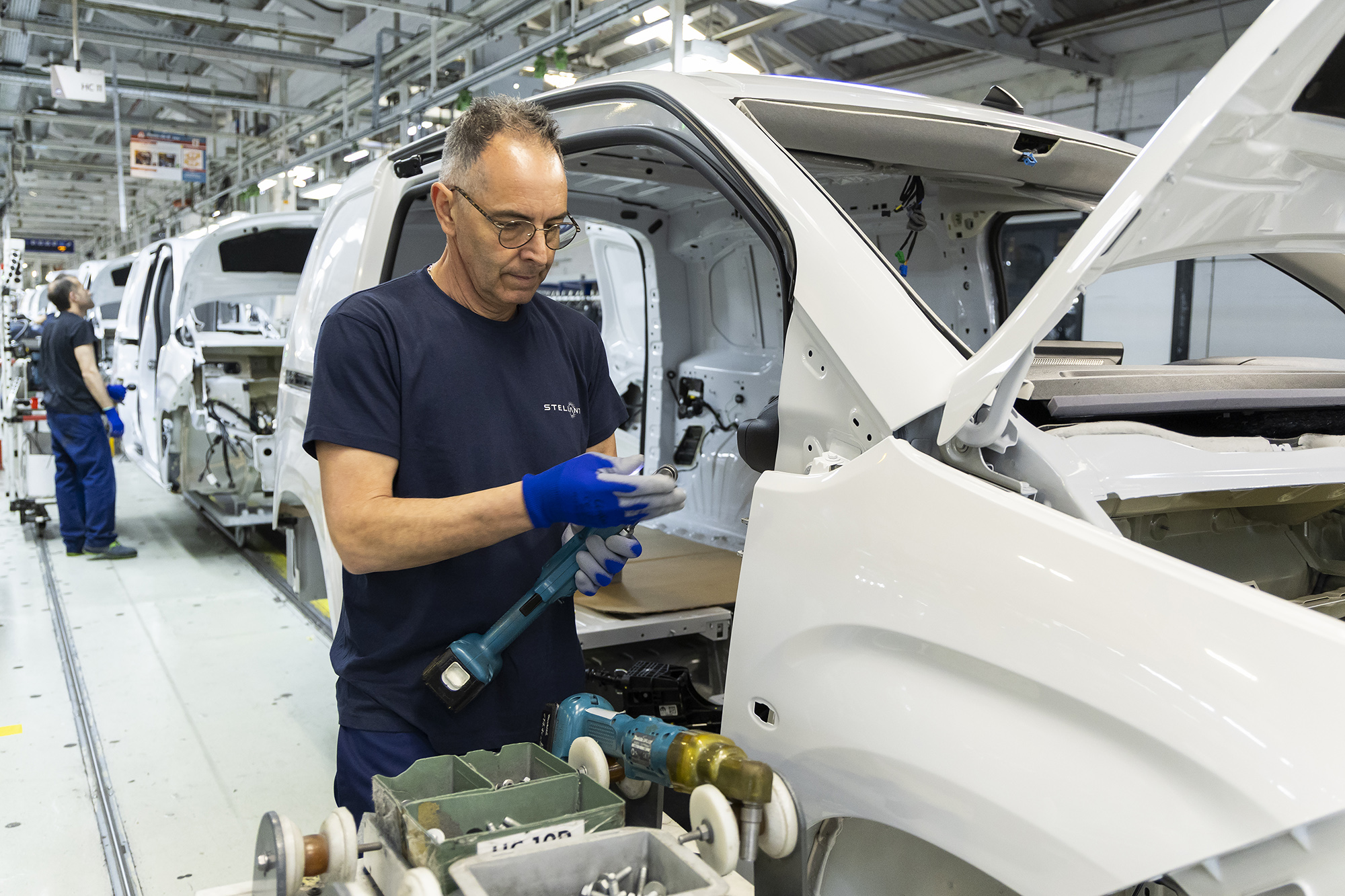
Um leigo que veja estes furgões ligeiros na linha de montagem apenas começa a identificar as distintas marcas aqui produzidas no momento da colocação do para-choques, mas a diferenciação começa logo na ferragem, com a construção da estrutura, altura em que é cravado o número de chassis.
Como elementos distintivos seguem-se a grelha, faróis, volante, revestimento dos bancos e algumas outras especificações de equipamento. E, claro, no símbolo, consoante seja um Citroën, Fiat, Opel ou Peugeot. Todos partilham a plataforma, a carroçaria e, no caso das respetivas versões elétricas, motor e bateria.
Foi precisamente um e-Berlingo que, em 2022, alcançou a unidade 15 milhões em Vigo, cuja abertura antecedeu Mangualde em apenas quatro anos, datando de 1958. Já em Portugal, necessitou-se de 50 anos para construir o carro um milhão nesta fábrica onde se montaram exclusivamente modelos Citroën até 1998, incluindo as unidades de um carro de corrida para vários países do mundo, o Saxo Kit Car, com o qual se estreou o reputado campeão do mundo de ralis, Sébastien Loeb. Outros made in Mangualde foram o Mehari, Visa, Dyane e DS (popularizado em Portugal como “boca de sapo”), e mais alguns Citroën.
Em 2026, surgirá a unidade dois milhões. Terão então passado apenas 14 anos desde a unidade um milhão na fábrica beirã, o que demonstra a intensificação do ritmo de produção, sobretudo a partir desta nova geração dos furgões da Stellantis, lançada em 2018, e que tem vindo a somar recordes de produção, esperando a empresa atingir nos 12 meses deste ano um total de 92 mil unidades.
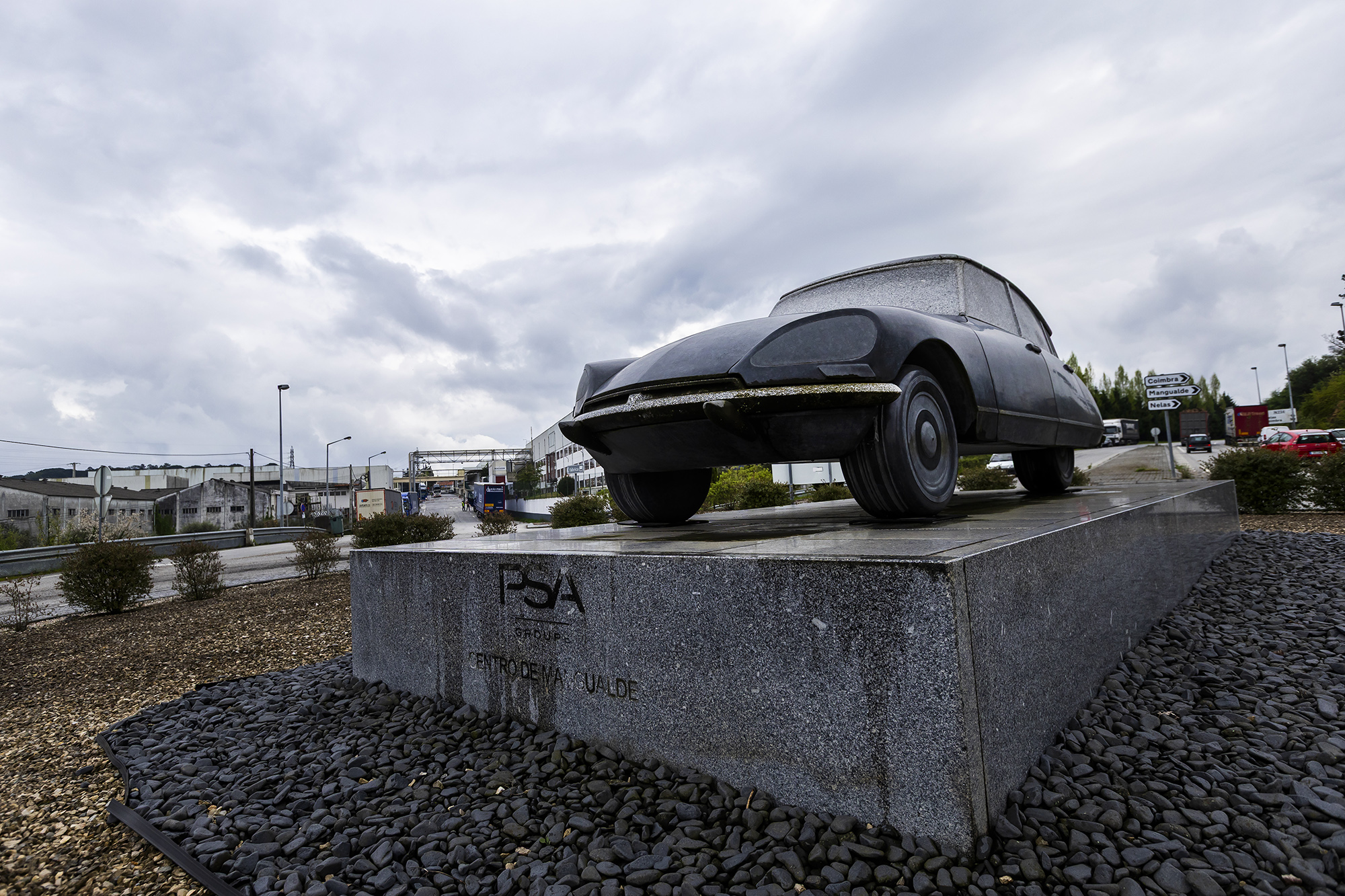
Passo a passo onde o automóvel português do presente já é elétrico
Para este novo momento histórico, a chegada do automóvel elétrico (numa geração dos furgões lançada em 2018), a Stellantis Mangualde encabeçou uma agenda mobilizadora do PRR (GreenAuto), num total de 119 milhões de euros destinados a 37 empresas, bolo financeiro em que um terço cabe à fábrica onde nascem os Citroën ë-Berlingo e ë-Berlingo Van, Peugeot E-Partner e E-Rifter, Fiat e-Doblò e Opel Combo-e. No fundo, o mesmo modelo, mas com diferentes marcas e em versões comercial e ligeiro de passageiros, e que asseguram a longevidade da fábrica de Mangualde um pouco para lá de 2030, assegura Múcio Brasileiro.
O diretor, a par do responsável pela montagem, Rui Oliveira, guiam o ECO/Local Online ao longo das várias fases da produção automóvel. O ex-líbris, desde meados do ano passado, é a secção designada “battery shop”. Esta determina cuidados especiais no tratamento de elementos elétricos em alta tensão. Ali, há uma zona designada L0, de exigência técnica mais moderada, similar a um normal trabalho de eletricista, e depois a zona L5, com corrente industrial, de média/alta tensão, identificada a azul, onde poderá haver risco de vida.
“Ali é onde nós ligamos a bateria e ela fica em carga. Passa a estar ativa. Até esses coletes estão proibidos, por causa da eletricidade estática”, explica Rui Oliveira, apontando para o equipamento de segurança que vestimos para efetuar esta visita. “Os colaboradores têm de vestir equipamento específico para trabalhar naquela área”, acentua o responsável pela montagem.
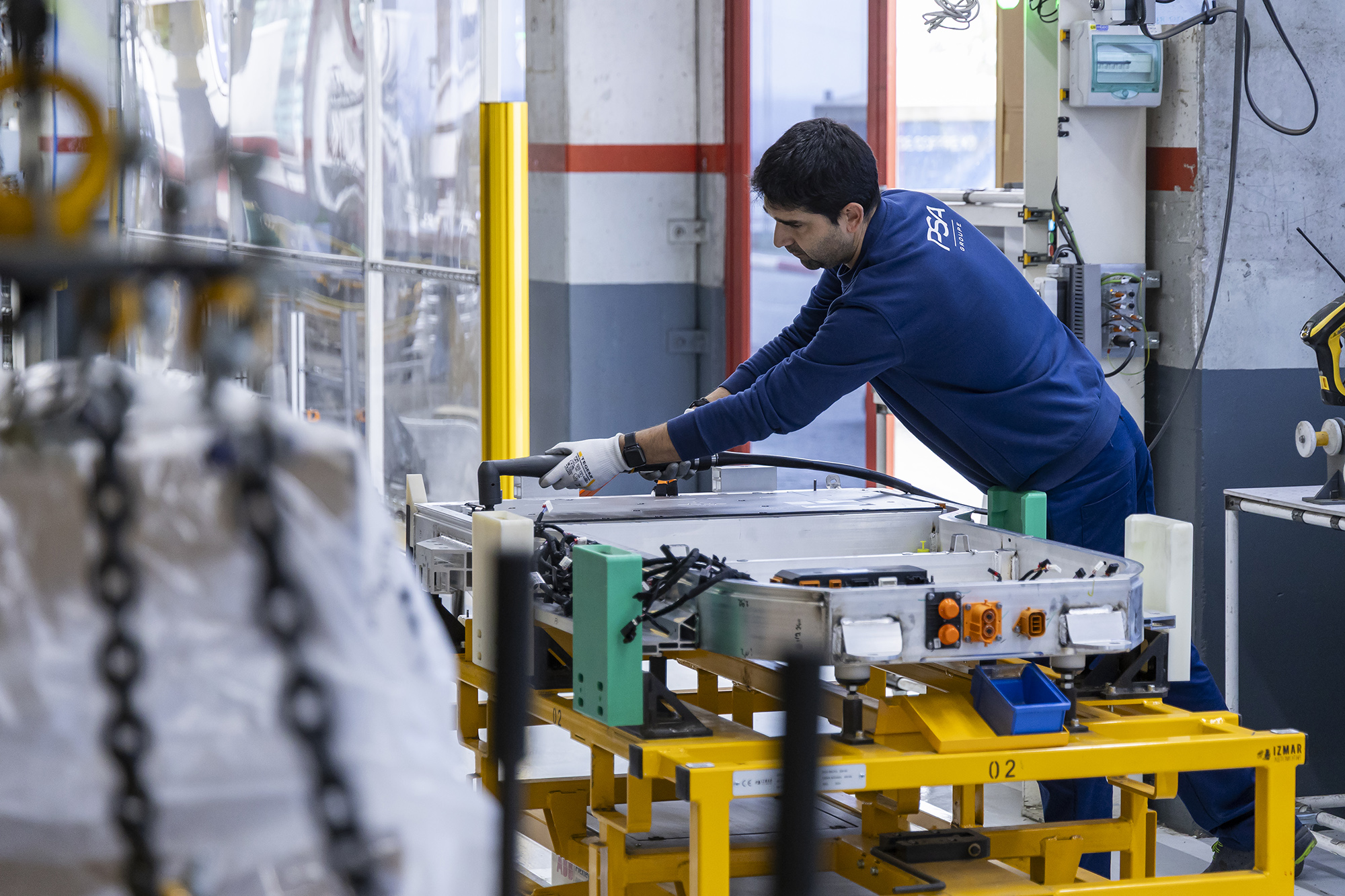
No conjunto do módulo elétrico há um opcional que elevou a complexidade do processo, uma bomba de calor, equipamento específico para mercados com temperaturas muito baixas. “A bomba de calor tem mais operações. Nas pré-séries, nos testes, tínhamos pedido para não sair logo um carro com bomba de calor. O primeiro carro que fizemos tinha bomba de calor. Pronto, já ficámos testados”, diz Rui Oliveira.
Para a “battery shop” foram selecionados funcionários da fábrica a quem era reconhecida aptidão para se adequarem tecnicamente a esta área. Para os lugares que ocupavam houve novas admissões, explica Rui Oliveira. “Aqui estão as pessoas que achamos que têm cuidados e consciência do tipo de trabalho. Escolhi lá em cima, na linha, os mais conscientes do tipo de trabalho. É preciso ter consciência dos riscos que envolve realizar a bateria. Não podemos facilitar”, diz. “Mais destreza, mais foco, mais atenção”, acrescenta Múcio Brasileiro, reforçando a exigência trazida pelas versões 100% elétricas a uma fábrica onde se produz estes furgões desde 1998.
Entre os passos realizados por cada operador está o aparafusamento dos módulos. Para tal, recebem os parafusos de um doseador. “No final de realizar a bateria, não pode sobrar, assim como não pode faltar”, realça Rui Oliveira. O carro elétrico impôs ainda maior precisão ao controlo de qualidade, salienta.
“A formação durou muito tempo”, acrescenta. “Tivemos a formação prática aqui. [Os trabalhadores selecionados] foram a Vigo ver ver fabricar o carro, as pré-séries, e regressaram já com o know-how e experiência do que viram lá fazer”. Ao todo, há 20 técnicos alocados ao processo, além de mais 44 funcionários com habilitação, explica Rui Oliveira. “Temos as pessoas todas identificadas. De vez em quando vêm cá, começam a fazer uma bateria, um posto. Isto dá-nos destreza para mantermos polivalência. Se algum dos colaboradores ficar doente, precisamos rapidamente de o substituir. Não posso parar a produção.”
De entre os imprevistos está desde um caso individual de um trabalhador até, como ensinou a história recente, uma pandemia. E dessa, Rui Oliveira recorda ter vivido, em 2020, uma situação “complicadíssima” na área que tutelava, a de projetos de inovação. Pela primeira vez em quase seis décadas, a fábrica produziu algo que nada tinha a ver com automóveis: máscaras. Um teste que acabaria por não passar disso.
Mas Mangualde não deixou de ser um caso de sucesso nesses tempos. “Foi a primeira fábrica do grupo Stellantis a retornar a produção” após a primeira paragem da pandemia, salienta o diretor. Primeiro, um só turno (um regresso forçado ao início dos anos 90), uma semana depois, o segundo turno, sempre com a regra de distanciamento de dois metros e a cantina com lugares de refeição transformados em cubículos de acrílico. “Sempre fomos identificados como fábrica modelo, até para outras indústrias. As pessoas vinham cá ver como estávamos a fazer”, conta Sofia Canez, uma decana da comunicação da unidade beirã.

Regresso do Opel Combo e a Fiat em estreia
Pelas dimensões, a própria metodologia de trabalho é distinta das demais fábricas do grupo Stellantis, com a logística separada da produção, chegando as peças à linha de montagem em pequenos robôs autónomos que se guiam por linhas amarelas no piso até atingirem o posto de cada trabalhador. A marca, a versão e a tipologia (passageiros ou comerciais) determinam o tipo de peças que chega em cada robô.
Observando a linha de montagem, vemos Citroën, Fiat, Opel e Peugeot alinhados e misturados, e nisso o lote de identificação de peças é determinante, para não colocar o volante de um Peugeot Partner num Opel Combo, por exemplo.
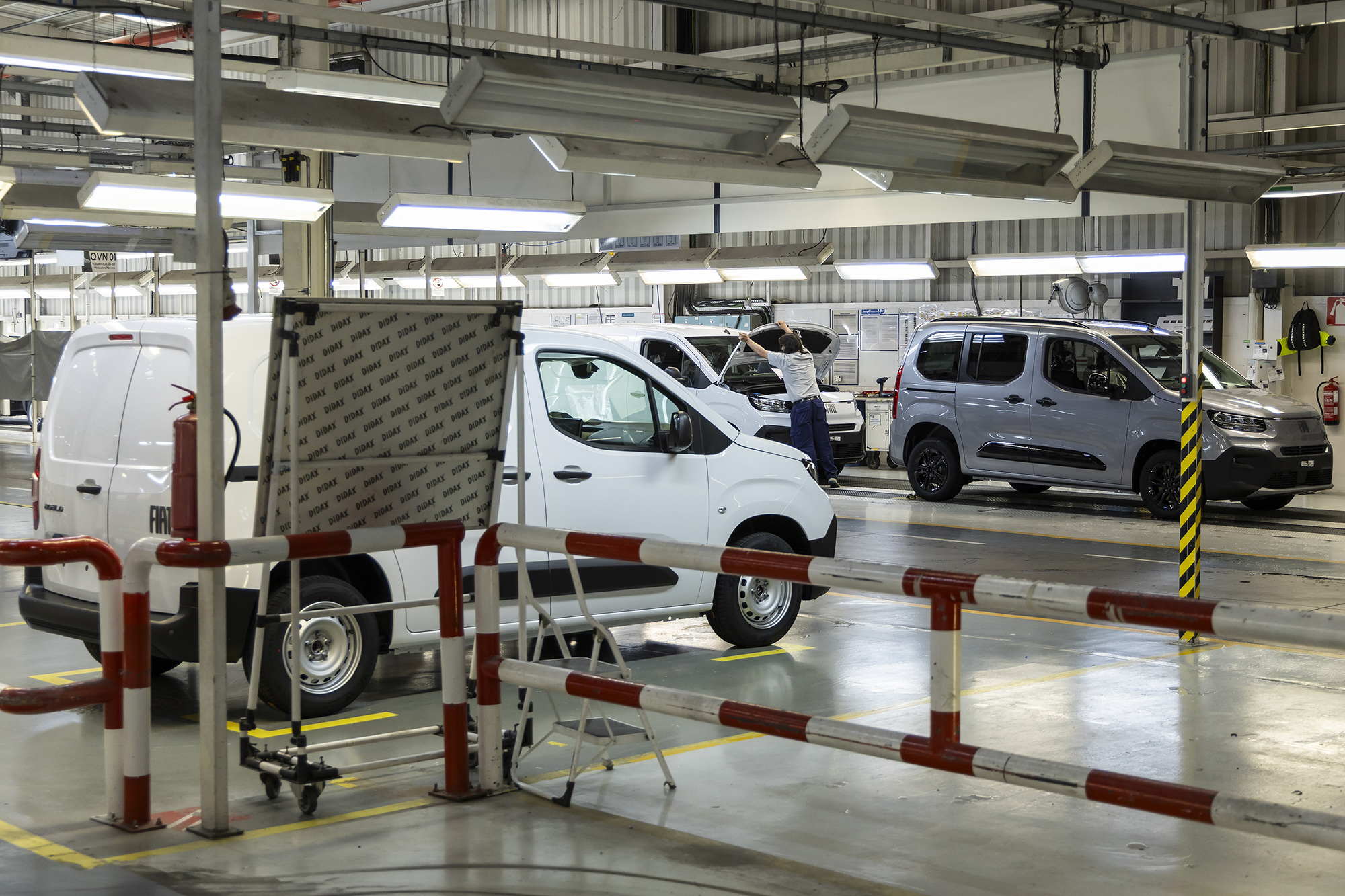
Os componentes entregues são exatamente os necessários para montar um carro. “Reduz a necessidade cognitiva e a margem de erro” numa linha onde existem mais de 650 configurações de carros, frisa Múcio Brasileiro. “A montagem é um processo sobretudo manual”, explica o diretor e “um processo muito minucioso, muito ao detalhe. O homem é essencial à nossa linha de produção”.
E, de facto, os robôs estão lá para apertar amortecedores e pouco mais. Em breve, haverá um para verificar a qualidade da montagem de fios e parafusos na parte inferior do furgão, para já um “estagiário” ainda em testes na zona dos elétricos.
De entre as quatro marcas que aqui estão por força da consolidação de marcas automóveis no grupo Stellantis, o caso da Opel, com o seu Combo, é um caso peculiar. A marca e o modelo estrearam-se em Mangualde em 2019, beneficiando esta fábrica da aquisição da Opel pela PSA – Peugeot/Citroën, que depois a levou consigo para dentro do grupo Stellantis, nascido com a fusão da PSA com a Fiat/Chrysler.
Mas o Opel Combo já foi, noutros tempos, ícone da produção automóvel nacional, na Azambuja, numa fábrica abandonada pela Opel por uma diferença de preço unitário inferior a 500 euros face a Saragoça, um caso laboral traumático com cerca de duas décadas na vida da vila da Azambuja, às portas de Lisboa.
EM 2018, a nova geração dos modelos chegou a Vigo e a Mangualde, levando à criação de um quarto turno na cidade galega, com mais 900 pessoas contratadas, e ao reforço da equipa portuguesa em mais de 200 trabalhadores. Agora, são já cerca de 900 trabalhadores em Portugal.
Dos homens a empurrar o esqueleto do 2CV à total automação atual
A produção de cada unidade tem o seu passo zero na ferragem, onde nasce a estrutura. Dali passa à pintura, hoje totalmente automatizada, ao contrário dos tempos do 2CV.
Dessa altura, José Ferreira recorda as mãos humanas que empurravam as gruas com o esqueleto do 2CV, pintavam à mão cada painel e depois levavam cada unidade num charriot até à estufa, de onde as retiravam após cozer. Quando começou a pintar os Citroën AX, há 30 anos, José, acabado de chegar à empresa — na qual entrou com a experiência de pequenas oficinas na cidade, após regressar de França, onde esteve emigrado com os pais — e hoje o funcionário mais antigo da Stellantis Mangualde, tinha de dar cor a 50 carros por dia. Ou até mais, caso desse lote saísse algum por defeito, conta-nos. “Às vezes acontecia que corria mal. Tínhamos de dar sempre os nossos 50 carros.”
Mas se na altura a pintura era executada a partir de baldes de 25 litros de tinta, hoje é robotizada, e já permite atingir 125 automóveis por dia. Também os parâmetros de qualidade evoluíram, impondo uma limitação de cores em Mangualde. Só branco, preto e cinza, para já.
“Se vir outra cor na estrada, não foi produzido em Mangualde”, diz-nos Múcio Brasileiro. Com um processo que aplica apenas uma camada, ao passo que em Vigo há “duas demão” em cada carro, a unidade portuguesa precisa de afinação especial para cada nova cor.
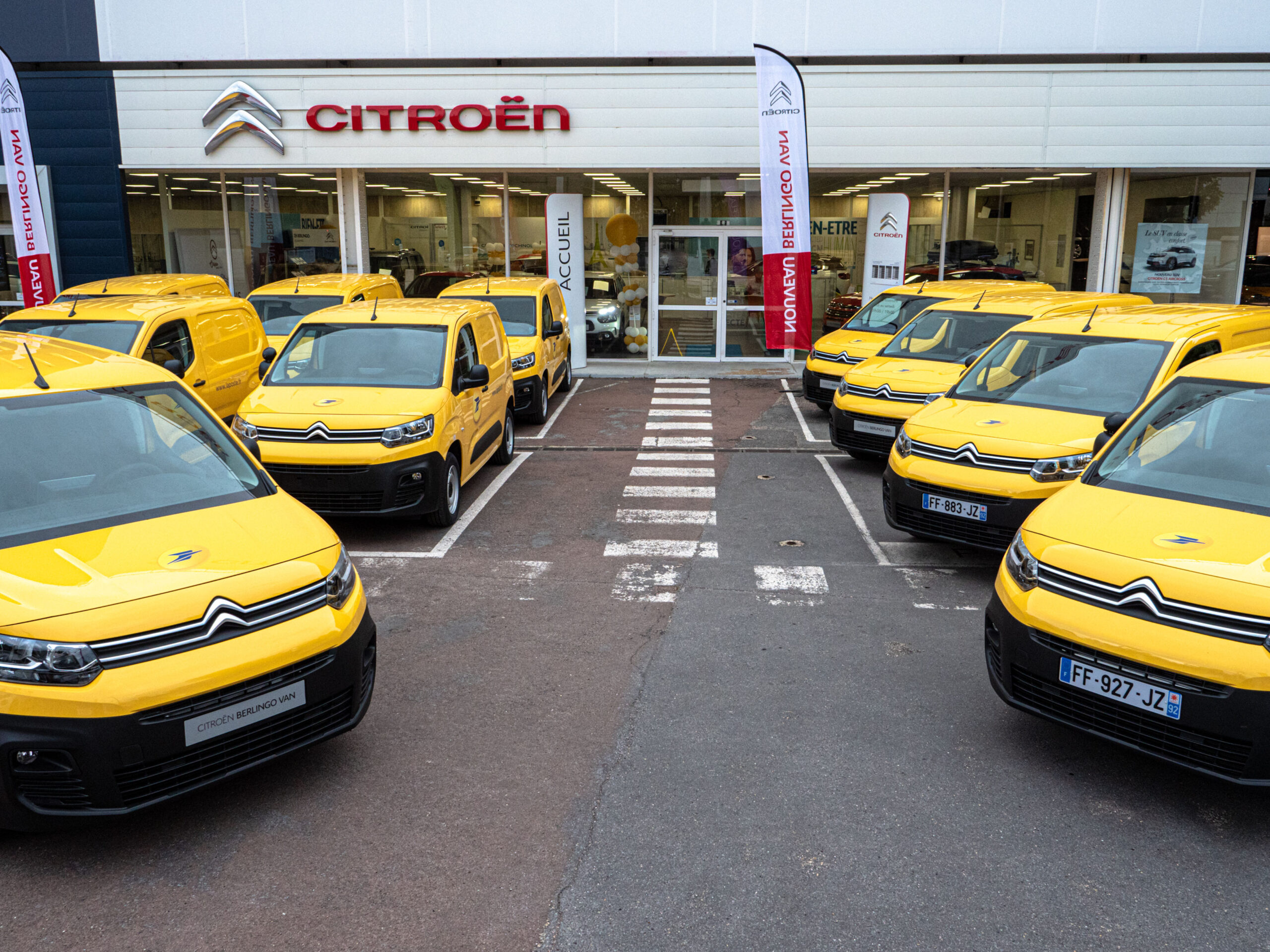
A exceção são os carros feitos à medida. Como o vermelho dos CTT ou o amarelo da empresa de correios francesa La Poste, que já foram feitos em Mangualde, e para os quais haverá nova remessa em breve, logo que esteja testada o RAL (sistema de cores) desse amarelo, diz-nos Rui Oliveira.
Outra cor específica saída daqui foi o verde “militar” com que foram pintados os furgões adquiridos pela NATO, recorda José Ferreira, identificando-a como a sua preferida em 30 anos a dar a pintura original a automóveis em Mangualde.
Chegados ao piso inferior da fábrica, atingimos o centro da eletrificação, uma área de 800 metros quadrados que já pertenceu à logística (deslocada para outro pavilhão) e que no ano passado foi reconvertida para daqui sair o kit específico dos furgões elétricos.
Também no piso inferior está o “berço” da parte mecânica dos veículos, com motor, caixa de velocidades, transmissão e depósito de combustível. Este não é, naturalmente, necessário nos elétricos. Para estes há uma porta específica para tomada elétrica, a primeira diferenciação nestes modelos na sequência da construção de cada carro.
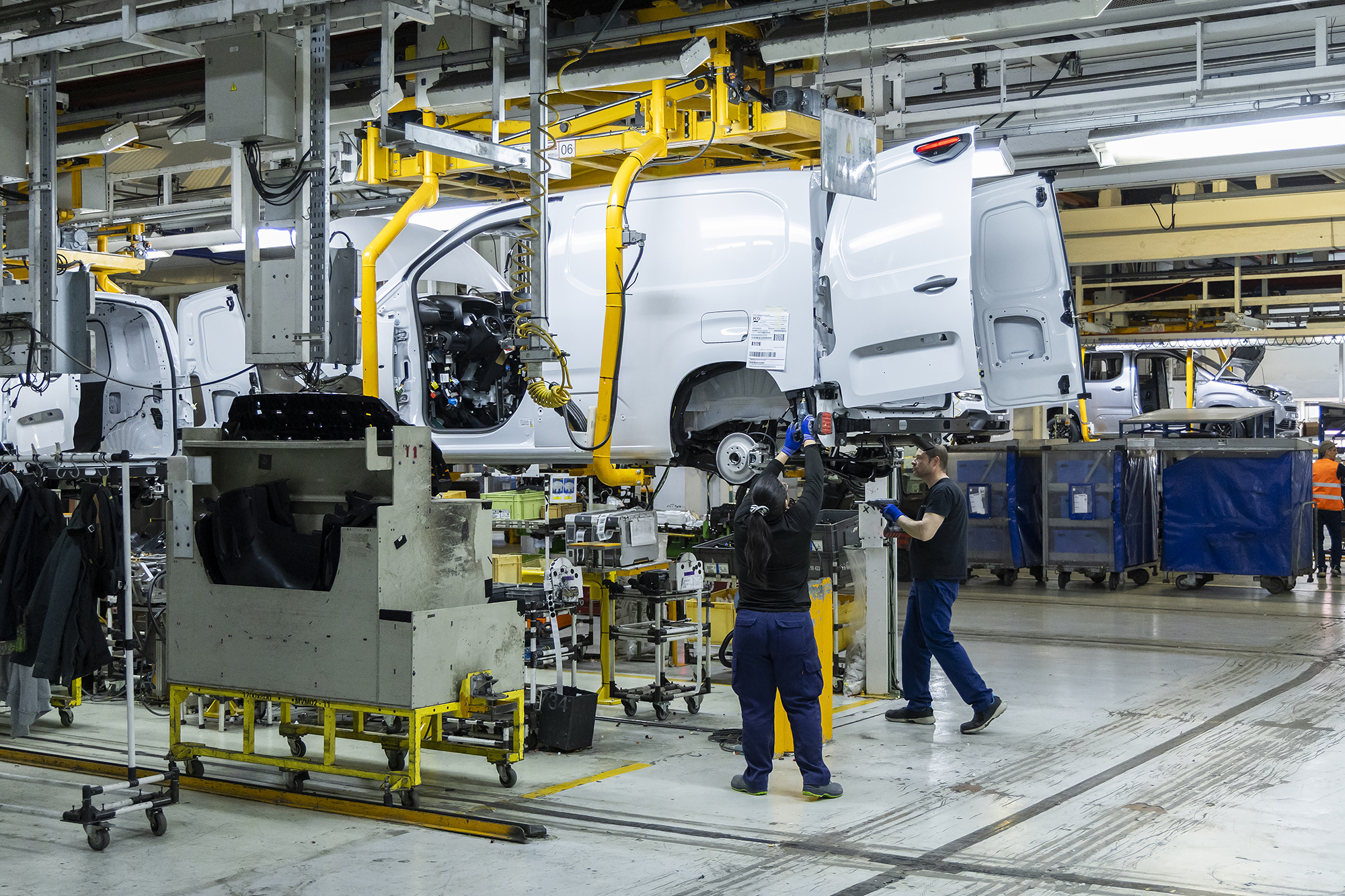
Outra característica distinta entre versões, no caso as comerciais e de passageiros, é a porta traseira da bagageira, um caso onde desponta a proverbial capacidade do português em ‘desenrascar’. Nos comerciais há portas de abertura em par na bagageira, necessitando de adotar os batentes no tejadilho e no piso. Noutras versões, há uma porta única que abre para cima, como num carro convencional, ficando-se com o batente apenas de baixo.
Ora, com os dois tipos de tejadilho exigem-se moldes da carroçaria distinto, e isso era um constrangimento para Mangualde, onde o espaço é limitado. Daí, surgiu o ‘ovo de Colombo’ beirão para propor à Stelantis: “A nossa proposta foi termos só um tejadilho. Estamos a falar em moldes de estampagem que são sempre muito caros, na manutenção, na repetibilidade. Ao fazermos duas peças de estampagem em moldes diferentes, temos que garantir que são iguais. No processo de ferragem têm que casar no mesmo sítio. Dissemos ‘todos têm que levar os mesmos furos’”, conta Rui Oliveira ao ECO/Local Online.
“Perguntaram ‘então e como é que tapas na montagem?’”. A solução era simples: “põe-se um autocolante, que não choca ninguém”, dispararam os técnicos portugueses. “Já tínhamos tentado fazer na versão anterior, mas como os moldes já estavam construídos, já não fomos a tempo. Nesta versão, propusemos isso, foi validado, está até hoje. O tejadilho vem sempre furado, só ficamos com um tipo de tejadilho”.
E assim, em Mangualde deixou de haver um problema bicudo, de como acomodar os moldes para os dois tipos de tejadilho. A solução, explica, “vem do terreno, da experiência das pessoas, dos nossos colaboradores, que nos vão passando estas informações, e nós vamos transmitindo”.
Assine o ECO Premium
No momento em que a informação é mais importante do que nunca, apoie o jornalismo independente e rigoroso.
De que forma? Assine o ECO Premium e tenha acesso a notícias exclusivas, à opinião que conta, às reportagens e especiais que mostram o outro lado da história.
Esta assinatura é uma forma de apoiar o ECO e os seus jornalistas. A nossa contrapartida é o jornalismo independente, rigoroso e credível.
Comentários ({{ total }})
Como a última morada do Citroën 2 CV se tornou berço de 90 mil carros na Stellantis Mangualde
{{ noCommentsLabel }}