A FFI e a DCSI Pro são empresas do mesmo grupo, mas também parceiras no desenvolvimento de linhas de produção automáticas que querem ajudar o calçado português a ser “referência internacional”.
“Fazer mais sapatos, em menos tempo, e com maior versatilidade”. A resposta ao mote lançado pelo ministro Adjunto e da Coesão Territorial, Manuel Castro Almeida, concentra-se numa área industrial de 13.500 metros quadrados em Estarreja, onde duas empresas “irmãs” têm juntado know-how para desenvolver “mini-fábricas” que tragam maior produtividade, mais qualidade do trabalho e, no final, mais dinheiro a um dos setores tradicionais da economia portuguesa: a indústria do calçado.
Do design ao produto final, passando pelos processos de corte, costura, cardagem e colagem, é nas instalações da DCSI Pro que estão a ser desenvolvidas as primeiras soluções tecnológicas de robotização do projeto FAIST – Fábrica Ágil, Inteligente, Sustentável e Tecnológica, uma de duas agendas mobilizadoras para o setor do calçado enquadradas no Plano de Recuperação e Resiliência (PRR) e que conta com um investimento de 50 milhões de euros.
É Florbela Silva, coordenadora do FAIST e diretora da unidade de Inovação e Fabrico Digital do Centro Tecnológico do Calçado (CTCP), outro dos 43 parceiros envolvidos no projeto, que nos acompanha na visita à DCSI Pro. Nesta empresa estarrejense, em que 32 trabalhadores fabricam diariamente equipamentos de automação e robótica industrial, estão expostos quatro protótipos que, embora ainda não possam ser comercializados, já estão prontos a laborar.
“Podemos dizer que temos aqui quatro mini-fábricas”, que resultam do “casamento perfeito” entre os desafios e os constrangimentos identificados no plano estratégico do cluster do calçado 2030 e o know-how das empresas de tecnologia em Portugal, afirma Florbela Silva.
O primeiro equipamento que nos apresenta é a linha integrada multiproduto, de todos o mais fácil de perceber a finalidade só pelo nome. Lado a lado, vemos uma forma branca de uma bota e outra de uma sapatilha, enquanto o robô simula a produção do calçado numa delas e, de seguida, ajusta-se automaticamente ao próximo modelo, diferente do primeiro. Em resumo, esta máquina permite, segundo a coordenadora do FAIST, “a produção de calçado de diferentes tipologias ao mesmo tempo na linha produtiva, sem que tenha sempre de ir alguém ao robô programar”, e mantendo, ainda assim, processos tradicionais de cardagem automática.
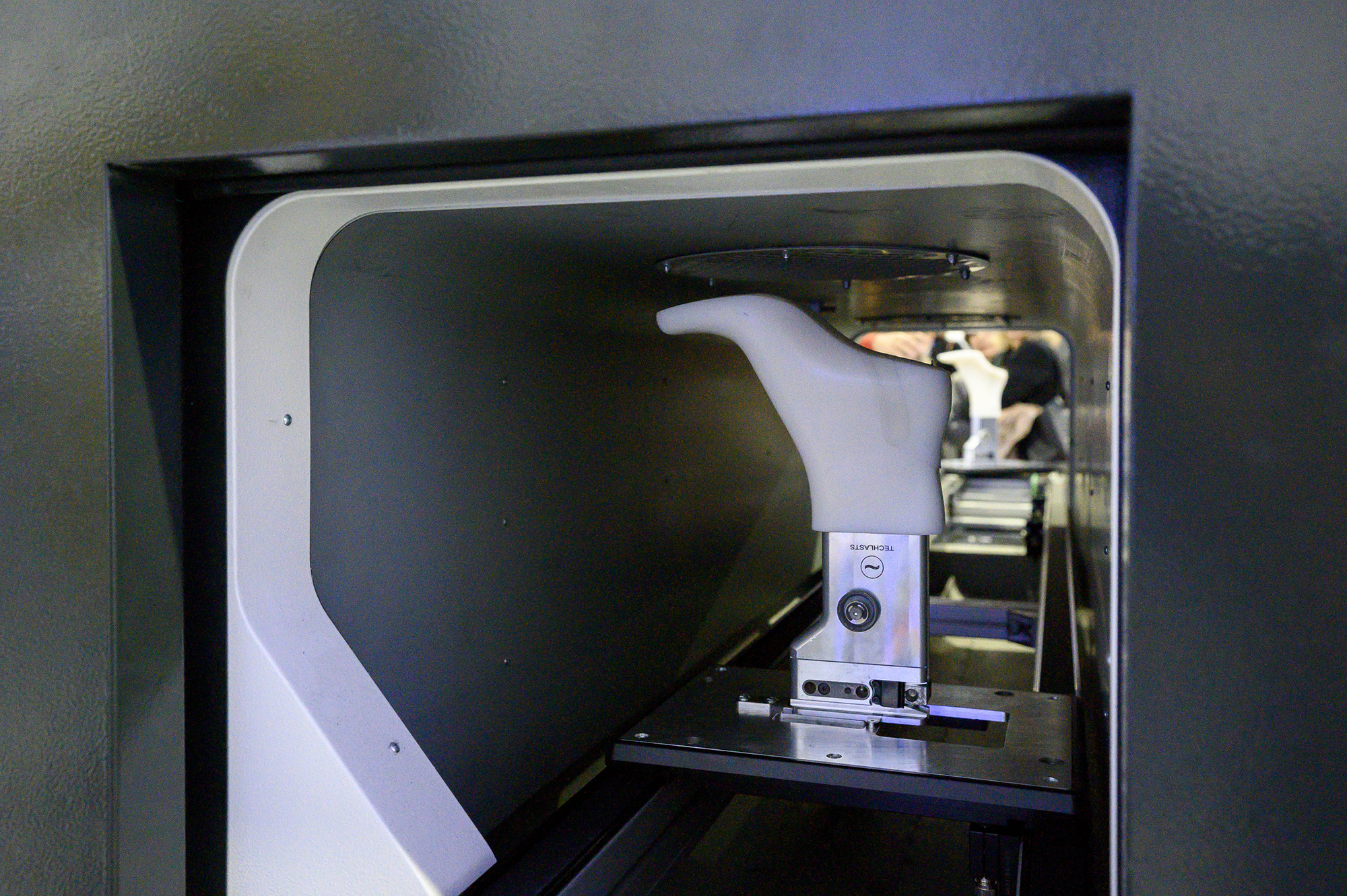
Avançamos para a “mini-fábrica” seguinte, que, nas palavras de Florbela Silva, é “uma tecnologia inovadora, bem como o produto que resulta dela”. Esta máquina, não sequencial em relação à anterior, faz “injeção direta ao corte”. Ou seja, em vez de um processo tradicional em que a sola de um sapato é colada ou costurada à gáspea, temos um sistema que injeta a sola diretamente à gáspea, não é cosida nem colada. Além disso, o injetor também pode unir diferentes partes de uma gáspea, excluindo a necessidade de serem costuradas.
A responsável pelo projeto compara o funcionamento deste modelo com o processo de fazer um bolo. “Há as diferentes matérias-primas [os ingredientes], que depois são misturadas para fazer a injeção – um processo que se assemelha ao uso de um saco de pasteleiro, só que em vez de um bolo, é para dentro de um molde”, diz, ressalvando, contudo, que neste caso “é preciso fazer autonomização e programação, para perceber a quantidade de material necessário, os tempos do ciclo de injeção, etc”.
Mas o resultado final vai muito além de um sapato sem costuras. “Com esta solução, evitamos processos de costura e de colagem, gastamos menos dinheiro em colas e outros materiais e ganhamos tempo, além de que é mais sustentável”, assinala a responsável do CTCP, que nota ainda que é necessário apenas um operador nesta linha produtiva.
De tamanho consideravelmente mais pequeno que os anteriores, o terceiro protótipo é formado apenas por um braço robótico e ferramentas. Dependendo da operação – se é fazer a cardagem, se é dar cola –, o braço robótico vai buscar a ferramenta adequada ao processo que vai fazer na linha de produção, deixando de ser preciso ter uma pessoa ou um robô para cada uma das operações.
Neste caso, o braço robótico foi adquirido no mercado, pelo que a DCSI Pro apenas desenvolveu à medida as ferramentas a serem usadas pelo robô e programou a integração deste na linha produtiva. “Em vez de termos uma pessoa oito horas por dia a fazer uma operação – a dar cola, a fazer a cardagem, etc. –, o que as pessoas ficam a fazer é o controlo de qualidade e ensinar o robô a operar”, explica Florbela Silva.
A esta linha de produção pertence ainda outra máquina, que faz a carda para colar a sola à gáspea. Aqui é possível ver mesmo o equipamento a fazer a lixagem de um sapato, uma etapa necessária para que a cola adira ao material da gáspea e depois encaixe na sola.
Junto com Leonel Ferro, que há várias décadas trabalha ao lado do irmão Fernando nas empresas do grupo Fernando Ferro & Irmão, do qual a DCSI faz parte, seguimos para a quarta e última “mini-fábrica” em exposição. Trata-se de uma máquina de alta frequência, uma tecnologia aplicada também no setor têxtil, que “reduz a necessidade de costura na gáspea a quase nada”, diz-nos, enquanto nos mostra um modelo de gáspea em que só será preciso costurar a parte de trás. Espumas, telas, tecido TPU ou PVCs são exemplos de materiais em que podem ser “impressas” as gáspeas.
Esta linha produtiva “consegue reduzir a necessidade de mão-de-obra, sendo necessários antes técnicos com conhecimentos noutras áreas, como software ou robótica”, refere Leonel Ferro, sublinhando ainda que, ao “fundir” vários tipos de materiais, “facilita o design” e permite uma “flexibilidade muito grande naquilo que são as novas tendências de produção no setor do calçado”.
Entre equipamentos e maquinaria, software, linhas integradas de produção, produtos e componentes de calçado inovadores e unidades piloto de experimentação e demonstração, o FAIST tem em desenvolvimento mais de 80 resultados para modernizar as empresas de calçado. “10% deles, talvez 20%, já estão prontos para ser mostrados em feiras. Comercializados ainda não, porque o projeto tem mais um ano de execução. Daqui a 10 meses, sim”, estima a coordenadora Florbela Silva.
Por estarem numa fase mais avançada, as máquinas expostas na DCSI Pro já foram mostradas na SICAM, uma das principais feiras do setor que decorreu em setembro na cidade italiana de Milão. E, segundo Florbela Silva, o feedback das empresas estrangeiras lá presentes aponta para um interesse em adquirir a tecnologia que está a ser desenvolvida em Portugal, o que é um bom prenúncio para cumprir um dos objetivos do FAIST: tornar a indústria portuguesa do calçado numa “referência internacional”.
“O facto de estarmos a modernizar as empresas de calçado ajuda também a atrair novos mercados para o setor do calçado. Ou seja, além do interesse em adquirir os sapatos produzidos cá por marcas portuguesas, também têm interesse nas máquinas que produzem esse calçado. E há também marcas estrangeiras que colocam a produção no nosso país”, acrescenta a responsável.
Menos sapateiros, mais especialistas em robótica e software
Pôr máquinas a fazer sapatos reduz a necessidade de mão-de-obra, tal como apontaram Florbela Silva e Leonel Ferro. No entanto, o ministro da Coesão Territorial, que também visitou as instalações da DCSI Pro para ver em ação as tecnologias que pretendem modernizar a indústria portuguesa do calçado, rejeita que tenha como consequência mais desemprego.
“Vai mudar é o perfil das pessoas que estão a trabalhar. Vai ter menos a imagem do sapateiro sentado no banco – que já está a desaparecer – e vai ter técnicos, da área das tecnologias de informação, do digital, da robótica, dentro das fábricas de sapatos”, antecipa Manuel Castro Almeida ao ECO.
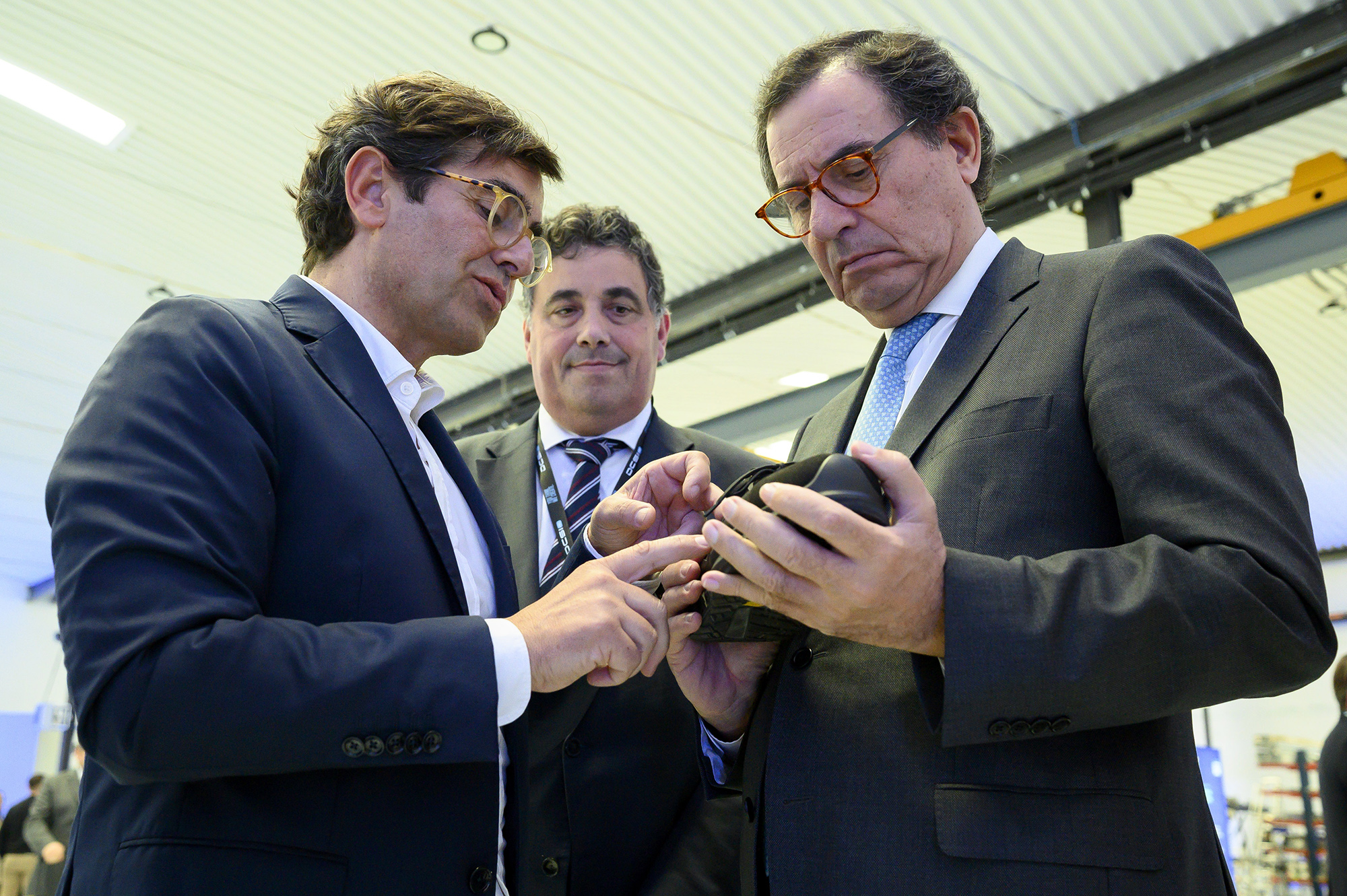
Um dos desígnios do FAIST é, aliás, a criação de 300 novos postos de trabalho, 100 dos quais altamente especializados, e que vão além do período do projeto. A coordenadora Florbela Silva detalha que estas áreas altamente qualificadas são “as de maior impacto e maior número de novos postos”, designadamente “o software e a programação de automação e robótica”. Não obstante, afiança que está prevista também a contratação de especialistas para a área do calçado.
Para a diretora da unidade de Inovação e Fabrico Digital do CTCP, nem a profissão de sapateiro se perde. “Uma máquina só pode ser criativa até um dado nível, mas o sapateiro é quem sabe fazer sapatos. A parte humana é imprescindível”, realça. E, ao sapateiro e à máquina, junta-se agora a inteligência artificial, que “já é aplicada no processo de design e também para inspeção e controlo de qualidade de um produto de calçado”.
Os dados mais recentes do BPstat, o portal de estatísticas do Banco de Portugal, relativos à indústria do calçado apontam para a existência de 1.801 empresas ligadas ao setor em 2023, um número que tem vindo a decrescer desde 2017 e que teve um volume de negócios de 2.288 milhões de euros, abaixo do pico de 2022. Além disso, o número de trabalhadores atingiu o valor mais baixo desde 2013, num total de 39.021.
Ainda assim, o recuo não é tão grande como o que se tem verificado no principal concorrente do mercado português na Europa. Em Itália, o número de empresas caiu 25,8% numa década, de acordo com o Eurostat, e a tendência estende-se ao nível da produção – de 202 milhões de pares produzidos em 2013 para 148 milhões em 2023, uma diminuição de 26,7%.
Com efeito, segundo a Associação Portuguesa dos Industriais do Calçado, Componentes, Artigos de Pele e Seus Sucedâneos (APICCAPS), Portugal foi o único país europeu a reforçar a produção na última década (+8%) – de 75 milhões de pares de calçado em 2013 para 81 milhões de pares em 2023 –, ultrapassando assim a Espanha e assumindo-se como o segundo maior produtor de calçado no continente europeu.
Para fazer face à maior competitividade do setor, que enfrenta também a forte concorrência da Ásia e do Brasil, e numa altura em que algumas das maiores economias da Zona Euro estão próximas da recessão – com destaque para a Alemanha, entre os maiores clientes da indústria de calçado portuguesa –, o ministro da Coesão Territorial destaca a necessidade de reinvenção de um setor cujo peso nas exportações totais do país caiu em mais de metade face a 2001, para 2,5% no ano passado, segundo uma análise do Gabinete de Estratégia e Estudos (GEE) do Ministério da Economia. Nas palavras de Castro Almeida, é preciso “transformar o conhecimento em faturas”.
O facto de estarmos a modernizar as empresas de calçado ajuda também a atrair novos mercados para o setor do calçado. Ou seja, além do interesse em adquirir os sapatos produzidos cá por marcas portuguesas, também têm interesse nas máquinas que produzem esse calçado. E há também marcas estrangeiras que colocam a produção no nosso país.
Tecnologia do calçado inspirada no automóvel e na eletrónica
Mas a visita não se ficou pela DCSI Pro. Mesmo ao lado da empresa, responsável pela implementação de soluções de automação e robótica industrial, está a Fernando Ferro & Irmão, S.A. (FFI), que produz os moldes para injeção e as formas brancas usadas nas “mini-fábricas” em exposição. Ambas são parte de um mesmo grupo de empresas – do qual faz parte também a Creatrix –, liderado por Fernando Ferro, sendo também parceiras no consórcio do FAIST.
“Aproveitando o know-how que temos também noutras áreas, como do setor automóvel, do alimentar ou da eletrónica, o que fizemos foi olhar e ver em que é que, nos processos tradicionais [de produção de calçado], podíamos usar a tecnologia para os modernizar, criar postos de trabalho menos duros e também transformar tarefas repetitivas em processos automáticos e dar formação às pessoas noutras áreas para poderem valorizar-se a elas próprias e também o produto”, conta-nos Fernando Ferro sobre o desenvolvimento das linhas de produção.
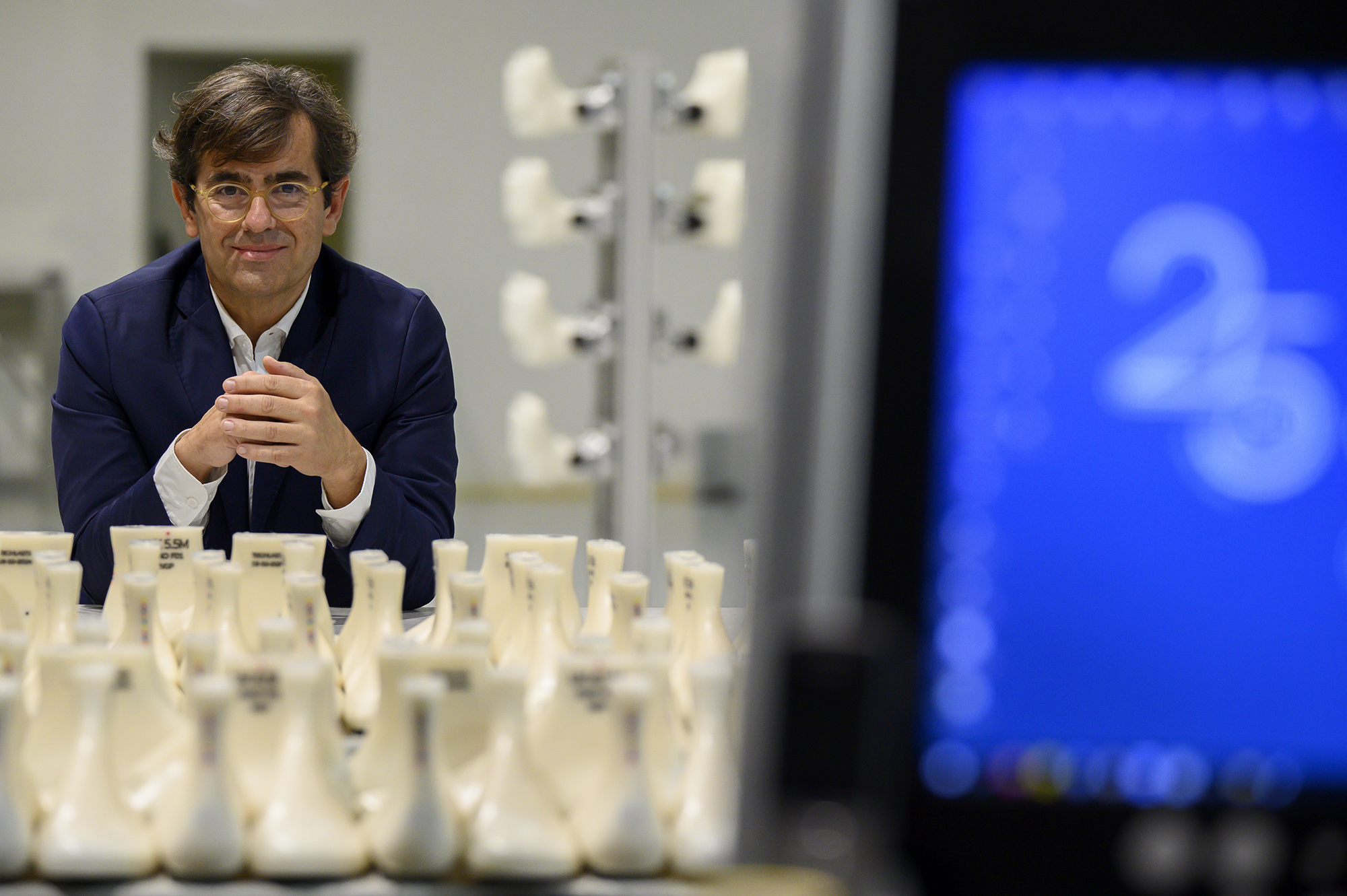
Fernando Ferro abriu o negócio há 27 anos em nome individual e só depois criou a Fernando Ferro & Irmão, S.A. com o irmão Leonel, contando hoje com mais de 90 trabalhadores. Embora o setor automóvel e a indústria no geral representem o “peso significativo” nas receitas de 5,6 milhões de euros alcançadas no último ano, o empresário – que está ligado ao setor do calçado desde os 14 anos, quando começou a trabalhar na Ecco – espera que o trabalho desenvolvido no âmbito do FAIST e de outros projetos permita “inverter” o cenário ou, pelo menos, pôr “lado a lado” a faturação da indústria dos sapatos e do mercado industrial em geral.
Prestes a contribuir para esse objetivo está uma multinacional asiática que vai instalar-se em Estarreja para produzir calçado para as grandes marcas desportivas, e com a qual a FFI está a negociar o fornecimento das linhas de produção automáticas (desenvolvidas fora do âmbito do FAIST). E, segundo Fernando Ferro, há outros projetos que estão em curso e com procura.
“Temos projetos em vias de finalizar que, se não fecharem ainda este ano, será no início de 2025”, disse o CEO do grupo, que, além do desportivo, vê no calçado de segurança ou de trabalho outra importante via de crescimento – ou não fosse a AMF, de Guimarães, um dos seus principais clientes.
Além das máquinas expostas, a DCSI Pro e a FFI têm outros quatro projetos em desenvolvimento no âmbito do FAIST. “Alguns não deram tempo de estarem montados, estamos à espera de materiais para começarmos a montagem. Estamos a andar bem e acredito que até ao final do ano devemos ter o esqueleto completo de todos os projetos que estamos a trabalhar, já montados e a continuar a integrar tecnologia, para podermos cumprir o nosso plano, que é até ao final do próximo ano termos os resultados concluídos”, sumariza Fernando Ferro.
Assine o ECO Premium
No momento em que a informação é mais importante do que nunca, apoie o jornalismo independente e rigoroso.
De que forma? Assine o ECO Premium e tenha acesso a notícias exclusivas, à opinião que conta, às reportagens e especiais que mostram o outro lado da história.
Esta assinatura é uma forma de apoiar o ECO e os seus jornalistas. A nossa contrapartida é o jornalismo independente, rigoroso e credível.
Comentários ({{ total }})
Estarreja “dá corda aos sapatos” na automação do calçado
{{ noCommentsLabel }}